Workshops
MACHINE SHOP
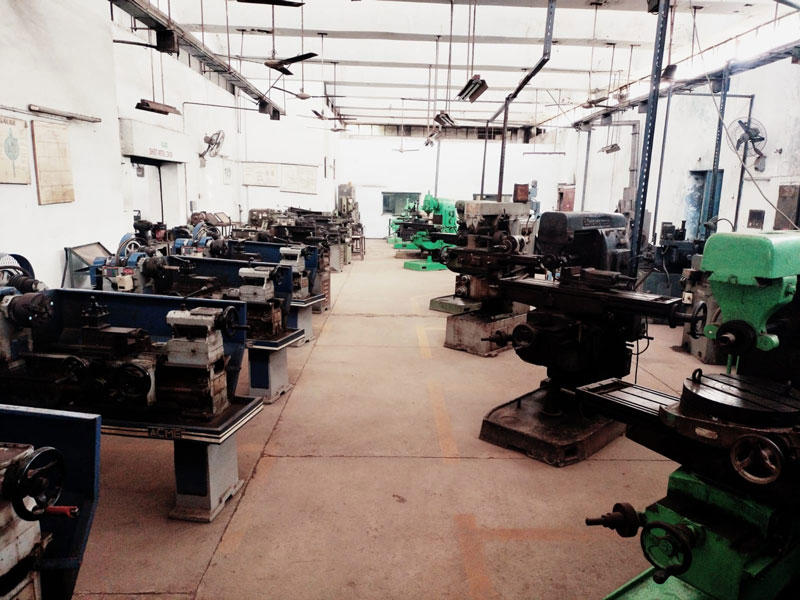
There are various types of machine available in Machine Shop.
Lathe Machine: – A lathe is a machine tool that rotates a work piece about an axis of rotation to perform various operations such as Facing, Turning, Drilling, Boring, Chamfering, Knurling etc. which is used to remove unwanted metals from the work piece to give desired shape and size. (Centre Lathe and Turret lathe etc.)
Milling Machine: – Milling is the process of machining using rotary cutters to remove material by advancing a cutter into a work piece. The metal removal rate is higher as the cutter has a high speed and many cutting edges (Horizontal Milling and Vertical milling etc.)
Drill Machine: – A drilling machine is a robust device used for advance and turn rotating drill bits into a work piece to create a round hole in or through solid materials. (Bench Drilling and Portable drilling machines etc.)
Grinding Machine: – Grinding machine, often shortened to grinder, is a power tool (or machine tool) used for grinding. It is a type of machining using an abrasive wheel. (Surface Grinding, Cylindrical Grinding, Tool & Cutter Grinding and Centreless Grinding Machines etc.)
Shaper Machine: – A shaper Machine is a reciprocating type of machine that is used for producing horizontal, vertical flat surfaces. The work piece is fixed on the table and the Ram holds the single point cutting tool.
Planer Machine: – Planer Machine is a machine in which unwanted material is cut from the work piece to produce a flat surface on the work piece. in this machine, more than one tool can be set and perform an operation.
Slotter Machine: – A Slotter machine is a machine tool in which material is removed for producing desired shapes. It is used for producing Machining cylindrical surfaces and flat surfaces.
WELDING SHOP
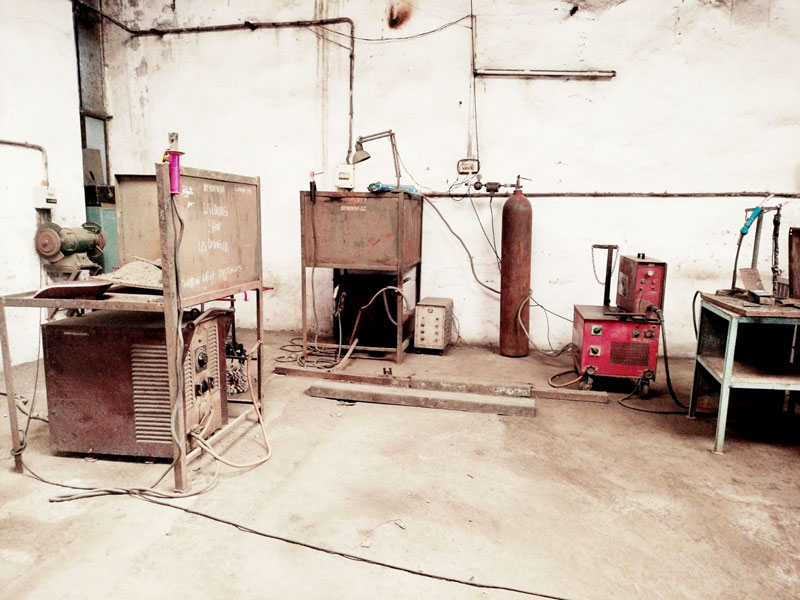
There are various types of Welding machine available in Welding Shop.
Oxy-acetylene Gas Welding: – Oxy acetylene welding uses a high-heat, high-temperature flame that is produced by burning a fuel gas (most commonly acetylene) mixed with pure oxygen. The base material is melted with the filler rod using a flame from the combination of oxy fuel gas through the tip of the welding torch (commonly called oxy acetylene torch welding).
Electric Arc welding: – Arc welding is a type of welding process using an electric arc to create heat to melt and join metals. A power supply creates an electric arc between a consumable or nonconsumable electrode and the base material using either direct (DC) or alternating (AC) currents.
Metal Inert Gas Welding: – Metal Inert Gas (MIG) welding is an arc welding process that uses a continuous solid wire electrode heated and fed into the weld pool from a welding gun. The two base materials are melted together forming a join. The gun feeds a shielding gas alongside the electrode helping protect the weld pool from airborne contaminants.
Tungsten Inert Gas Welding: – TIG stands for tungsten inert gas and is technically called gas tungsten arc welding (GTAW). The process uses a non-consumable tungsten electrode that delivers the current to the welding arc. An inert gas, typically argon, protects and cools the tungsten and weld puddle. TIG welding is similar to oxy-acetylene welding in that you use a filler material for build-up or reinforcement.
Spot Welding: – Spot welding is a resistance welding process. This welding process is used primarily for welding two or more metal sheets together by applying pressure and heat from an electric current to the weld area.